How the Supply Chain Act puts companies under obligation
The Supply Chain Act demands more responsibility from companies while offering new opportunities for efficient processes through digitalisation and automation.
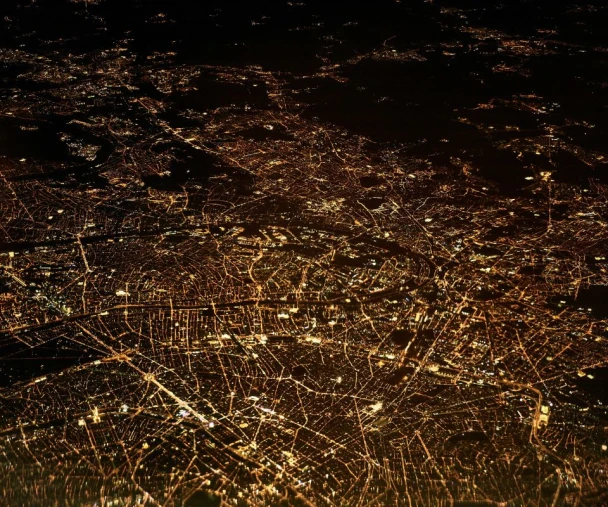
Since 1 January 2023, the Supply Chain Act has been in effect. This law aims to strengthen human rights along global supply chains and ensure that environmental protection standards are diligently upheld. But what does this mean in practice for companies? And how can automation help simplify processes while making them more transparent?
Responsibility grows: new regulations for companies
The Supply Chain Act requires companies to extend their responsibilities far beyond their own boundaries. They are now obliged to oversee the entire supply chain and ensure no violations of human rights or environmental protection norms occur. This means companies are now responsible not only for themselves but also for their partners and suppliers. Responsibility must be taken along the entire production path, from raw material extraction to the production of individual components.
Stricter requirements, greater due diligence
Currently, the Supply Chain Act applies to companies with more than 3,000 employees domestically. From 2024, it will also apply to companies with 1,000 or more employees. Responsibility no longer ends at corporate borders but extends across the entire supply chain. This requires companies to ensure their suppliers and partners meet legal requirements, gather relevant evidence, and document compliance.
Challenges and opportunities of digitalisation
Implementing this extensive new duty of care undoubtedly presents challenges. Documentation and monitoring demand time and resources, increasing administrative burden and costs. Fortunately, digitalisation and automation can simplify many aspects, reducing complexity and significantly easing these processes for companies.
Automation as the key to efficiency
The key to meeting new requirements lies in automation. Digital solutions can help companies streamline the process of collecting, storing, and archiving certificates. Automated workflows minimise manual effort, saving time and paving the way for smoother production processes.
The technical prerequisites for automation depend on the provider. Typically, automation clients are integrated as software into the company's existing systems. Secure interfaces, such as Restful APIs, enable these connections. However, it is essential that documents are available in digital format.
With solutions like FTAPI SecuFlows, the entire process can be mapped and automated. Since supply chains often involve sensitive data that must be recorded and stored, SecuFlows operates with encryption to prevent unauthorised access.
An example of certificate management automation could look like this:
Suppliers receive an automated email requesting them to submit relevant certificates.
An integrated link in the email directs them to a secure online form, such as FTAPI SecuForms, where required information and documents can be uploaded. Using supplier numbers, these submissions are automatically transferred into the company’s system and assigned to the corresponding supplier.
Automated reminders ensure timely renewal of certificates.
Certificates are centrally stored on the company’s server or system.
Certificates can be archived in virtual data rooms, such as FTAPI SecuRooms, making them easily accessible for audits without excessive administrative effort.
Digital whistleblowing systems a
Implementing the Supply Chain Act simply, securely and automatically!
Find out here how you can use FTAPI to quickly, efficiently and successfully integrate the requirements of the Supply Chain Act into your business processes.
s an additional option
The increased due diligence in supply chains may uncover issues along the way. It is crucial to have secure channels where employees, suppliers, or other external parties can report concerns without fear of retaliation or disadvantage. IT-supported whistleblowing systems, available 24/7 and ensuring anonymity, are a practical solution. FTAPI SecuForms offers automated setups for such systems, which can be implemented quickly and efficiently.
Conclusion: responsibility meets innovation
The Supply Chain Act introduces new challenges for companies but also provides opportunities for innovation. By leveraging digital solutions and automating processes, companies can comply with the law while avoiding unnecessary administrative burden. This not only ensures compliance but also offers a competitive advantage for those who skillfully embrace the potential of digitalisation.